Background
Eye injuries in the workplace can have severe consequences, including permanent vision loss. According to the CDC, over 2,000 workers sustain job-related eye injuries daily, leading to significant downtime and economic loss. Implementing proper eye protection and eyewash stations is crucial to ensure safety and compliance with OSHA regulations. This article outlines the requirements for eye protection and eyewash stations at your dealership and why they are critical.
The Law on Eye and Face Protection
Employees working in locations where there is a risk of receiving eye injuries such as punctures, abrasions, contusions or burns as a result of contact with flying particles, hazardous substances, projections or injurious light rays, which are inherent in the work or environment, shall be safeguarded by means of face or eye protection. Suitable screens or shields isolating the hazardous exposure may be considered adequate safeguarding for nearby employees. Note: Anyone at risk of an eye injury needs protection!
Types of Eye Protection
Employees are often exposed to hazards such as flying particles, chemical splashes and intense light from welding operations. These hazards make appropriate eye protection necessary.
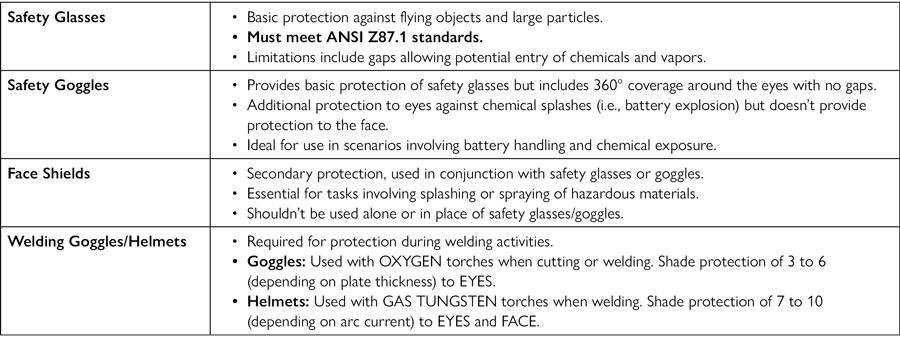
Can I Wear Normal Prescription Lenses/Frames Instead?
NO. Normal prescription lenses and frames DO NOT meet safety requirements, are not strong enough and haven’t been tested to ANSI standards. Prescription safety glasses that meet ANSI standards [ANSI Z87-2+] or over-the-glasses safety glasses/goggles may be worn as a substitute for safety glasses/goggles.
Eyewash Stations
Cal/OSHA requires eyewash stations (EWS) where employees may encounter corrosive chemicals and specifies requirements for eyewash stations, including accessibility and functionality criteria. Battery charging, battery filling, used battery storage and use/dispensing of corrosive chemicals or irritants are processes that require the installation of an eyewash station. In general, Cal/OSHA refers to ANSI standards as the widely accepted guideline for the proper selection, installation, operation and maintenance of emergency eyewash station equipment. Note: During routine inspections, remind employees to keep the area clear.
Does the Parts Department Need an Eyewash?
YES. A big box warehouse store with multiple outlets in California was cited by Cal/OSHA for failure to have eyewash stations. The employer appealed to the California Occupational Safety & Health Appeals Board (COSHAB) stating that the eyewash standard does not apply as the chemicals are merely unloaded, unboxed and placed on shelves in sealed containers by employees. COSHAB held that the employees could be exposed to leaks and spills from packages damaged in transit and when employees unpack these cases. Employees involved in cleanup in the warehouse where there is a spill have the potential of an eye injury from corrosive and irritating chemicals, hence the requirement of an eyewash in the warehouse.
Eyewash Station (EWS) Selection
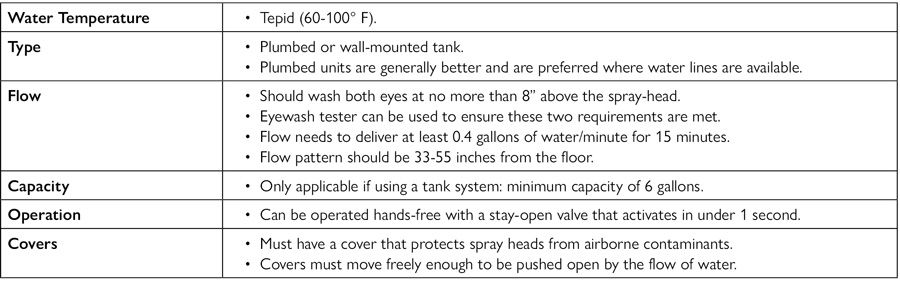
Eyewash Station (EWS) Location
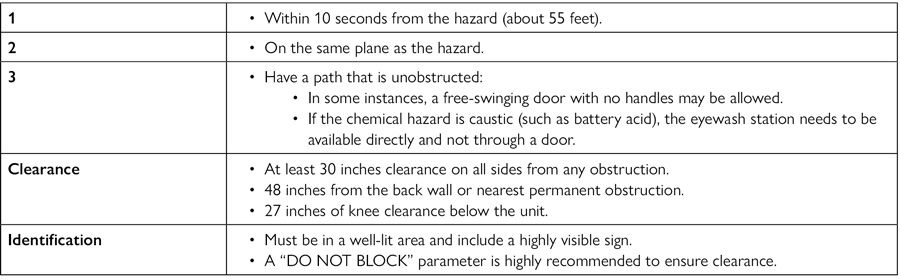
EWS Maintenance, Cautions and Common Misconceptions
Inspect and perform weekly activations. A weekly maintenance/activation log needs to be maintained, and 90-day flushes for wall-mounted units also need to be performed/documented.
- Any valves on the supply line to plumbed units need to have their handles removed.
- Water hoses, sinks, faucets, showers and eyewash bottles DO NOT comply with Cal/OSHA standards.
- Handheld drench units support but do not replace a dedicated EWS.
- A single step into an enclosure where EWS can be accessed is not considered to be an obstruction.
- HOWEVER, this must also meet wheelchair accessibility requirements where applicable.
- The PARTS department dealing with any chemicals that can cause corrosion, severe irritation or permanent tissue damage (battery acid) also needs a dedicated EWS.
Conclusion
Adhering to these guidelines for eye protection and eyewash stations is essential to safeguard your employees from potential eye injuries and ensure regulatory compliance. By implementing comprehensive safety measures, we can reduce the risk of injury and promote a safe working environment.
This article does not cover all necessary elements of the standard. We merely summarize some important elements.
Ref: CAL/OSHA: Title 8 CCR 5162, 3382 FED: 29 CFR 1910.151(c), 133 (a) (1) ANSI: Z87-1, -2+, 358.1-2014
DISCLAIMER: The contents of this newsletter are for informational purposes only and are not to be considered as legal advice. Employers must consult their lawyer for legal matters and EPA/OSHA consultants for matters related to Environmental, Health & Safety. The article was authored by Sam Celly of Celly Services Inc., who has been helping automobile dealers across the United States comply with EPA and OSHA regulations for over 38 years. Sam is a certified safety professional (No. 16515) certified by the National Board of Certified Safety Professionals. Sam received his BE (1984) and MS (1986) in chemical engineering, followed by a J.D. from Southwestern University School of Law (1997). Sam is a member of the American Chemical Society (No. 31176063), American Industrial Hygiene Association (No. 124715), and National Association of Dealer Counsel (NADC). Sam also serves on the Board of Orange County American Industrial Hygiene Association and on the California Industrial Hygiene Council (CIHC). Our newsletters can be accessed at www.epaoshablog.com. Your comments/questions are always welcome. Please send them to sam@cellyservices.com.